Thermoplastics Solve the Challenges of Water Disinfection using Sodium Hypochlorite
By David Guardia, Technical Services Manager, Ryan Herco Flow Solutions
There have been many important factors in the exponential growth of human lifespan over the past century – advances in medicine, nutritional awareness, and pharmaceutical discoveries – but perhaps one of the most significant factors is the ready availability of disinfected drinking water.
Disinfected potable water provides protection from pathogenic organisms including those causing cholera, polio, typhoid, hepatitis and a number of other bacterial, viral and parasitic diseases.
Disinfection may be accomplished by filtering out harmful microbes, but it is more commonly completed by adding disinfectant chemicals as the last step of purifying drinking water. In most developed countries, public water supplies are required to maintain a residual disinfecting agent throughout the distribution system to protect against microbial growth as water may remain for days before reaching the consumer.
Chlorination is the most common disinfection method and involves some form of chlorine or its compounds such as chloramine or chlorine dioxide. Chlorine is a strong oxidant that rapidly kills many harmful micro-organisms. Because chlorine is a toxic gas, there is a danger of a gas release and health concerns associated with its use. This problem is avoided by the use of sodium hypochlorite (NaOCL), which is a relatively inexpensive liquid solution that releases free chlorine when dissolved in water. Commonly known as chlorine or bleach, sodium hypochlorite is a strong oxidizer normally used as a disinfection agent. Because it is readily available, inexpensive and very effective, NaOCL is the most common water disinfection agent globally.
The same aggressiveness that makes sodium hypochlorite an effective disinfectant also makes it a challenging chemical to store, transport and apply properly. Most metals, including stainless steels, have very poor results when used to contain and transport sodium hypochlorite even in the standard low concentrations of 5.25% (consumer concentration) and 12.5% (industrial concentration). In steel, the highly aggressive chemical causes rust and corrosion. Thermoplastics are the preferred materials when building NaOCL fluid systems. Polyvinylchloride (PVC) and Polyethylene (PE) are inexpensive solutions for handling the standard concentrations. In higher concentrations (to 100%) PVDF and PTFE are excellent choices.
Besides its aggressiveness, sodium hypochlorite presents another challenge for fluid handling systems. This is its tendency to “outgas” which means as it decomposes, one of the by-products turns from liquid to gas. Sodium Hypochlorite solutions outgas because the NaOCL decays over time into a salt solution and generates gaseous oxygen in the form of bubbles. These bubbles accumulate in fluid system and can cause problems such as loss of prime in pump suction lines and ball valve damage. Higher sodium hypochlorite concentrations and higher ambient temperatures cause more outgassing. Even 1ml of active chlorine in solution can produce several cubic inches of gas.

Select a ball valve featuring an outgassing vent in the ball. Photo courtesy of Hayward Flow Control.
All NaOCL systems have common features including pipe, valves and fittings, pumps for transport, storage, chemical injection and instrumentation for monitoring.
We will look at each of these attributes individually for best system practices.
Pipe, Valves and Fittings
PVC or CPVC is the preferred piping choice for sodium hypochlorite concentrations under 20%. Follow the manufactures recommended installation procedures. In warm ambient conditions or direct sunlight, pipe insulation should be considered to minimize outgassing.
PVC valves should use FKM seals and PTFE seats or diaphragms. When using ball valves, they should have special ‘vented’ balls (available from most manufacturers) which prevent over-pressurization and damage from outgassing by venting the gas back upstream.
Storage Tanks
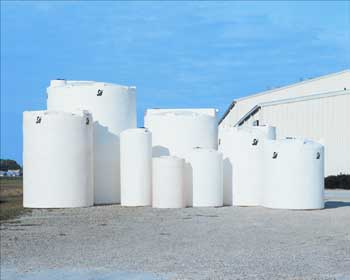
To Optimize NaOCL storage, eliminate UV rays and reflect sunlight to keep the tank cooler, select tanks made using opaque white high-density linear polyethylene (HDLPE resin). Photo courtesy of Snyder Industries.
Ultraviolet (UV) radiation not only degrades light sensitive chemicals such as sodium hypochlorite, but also has the potential to significantly damage the structural integrity of the plastic storage tank containing the NaOCL.
Smaller tanks should be placed out of direct sunlight to eliminate the UV issue.
With larger tanks, natural translucent polyethylene should be avoided because the UV rays will pass through the tank wall causing the problems noted. While some manufactures have promoted black pigmented tanks to block the UV rays, the heat generated by sunlight falling on the black surface can cause other issues such as excessive outgassing.
The optimum solution for NaOCL storage is opaque white high density linear polyethylene (HDLPE resin). This eliminates the UV rays and reflects the sunlight to keep the tank cooler.
Chemical Metering Pumps

Metering pumps are available in a variety of sizes for systems ranging from small water districts to large municipalities. Photo courtesy of Walchem Corporation.
The most common way of accurately dosing NaOCL into a potable water distribution system is to use a chemical metering pump. These pumps can inject small, precise quantities into high pressure piping systems to maintain free chlorine at a specific PPM level. Often, they are used in conjunction with a flow sensor which will control the output of the pump to proportional match changes in water flow rate and maintain the correct PPM dosage.
As sodium hypochlorite outgasses, bubbles may accumulate in the suction line and pump head causing loss of prime results in no pumping action, un-disinfected water and possible damage to the pump head.
Solutions for minimizing or completely eliminating loss of prime issues include:
- Keep the NaOCL solution cool by placing the pump and tank out of any direct sunlight and away from heat sources. Also consider insulation of the tank and metering pump suction lines. The cooler the solution of NaOCL, the less outgassing will occur.
- Reduce the sodium hypochlorite concentration if possible. Lower concentrations outgas less. Below 5% concentration, very little outgassing occurs.
- Install a vertical “stand pipe” at the pump inlet that rises above the level of the NaOCL tank and is properly vented at top. Any gas which builds up in the suction pipe will be automatically evacuated into the atmosphere before reaching the pump inlet.
- Manual or automatic air vent valves should be fitted to the discharge pipe work to aid in priming.
- A water flushing circuit “Teed” into the suction line will aid in flushing out any salt residue in suction lines and pumps.
Chemical Transfer Pumps

Choose mag-drive pumps that use high grade samarium cobalt (Sm2-Co17) magnets which have proven corrosion resistance to sodium hypochlorite. Photo courtesy of Iwaki America Inc.
Sodium hypochlorite is just as devastatingly effective at destroying mechanical pump seals as it is at corroding metals. Fluid transfer from bulk storage to point of use is best accomplished using seal-less magnetic drive pumps that have fluorinated thermoplastic heads. Mag drive pumps have no motor drive shaft seals which may decay and leak.
Even with seal-less mag drive pumps, over time the NaOCL can permeate the thermoplastic and attack lower grade magnets with disastrous results. Look for mag-drive pumps that utilize high grade Samarium Cobalt (Sm2-Co17) magnets which have proven corrosion resistance to sodium hypochlorite. Pump designs that feature Neodymium Iron Boron (Nd-Fe-B) or Barium Ferrite magnetics will have little or no corrosion resistance to NaOCL over time.
Instrumentation
Level Sensors: Large municipal water treatment systems often have remote bulk storage and smaller ‘day’ tanks at the point of use. Continuous level sensors (either ultrasonic or radar) can be placed inside the storage tanks to provide inventory control while smaller sensors are better suited in day tanks to provide demand control of the transfer pumps or in the case of an empty tank, stop automated pumping operations.

Chlorine analyzers are used to measure the residual chlorine in the water before its put into the distribution system. Photo courtesy of Georg Fischer Piping Systems.
Flow Sensors: Flow sensors are often used in the potable water lines to proportionally? ‘pace’ the chemical metering pumps and assure the correct amount of chlorine is injected as flow rate vary high and low. Without flow sensor control, a metering pump is manually adjusted to an average flow rate. When this occurs, the pump injects too much chemical when the flow volume is below average and not enough when it is above average. Flow control guarantees proper chemical dosage and minimizes cost from over dosage of chemical.
Chlorine Analyzers: Chlorine analyzers are used throughout several water treatment stages to measure free and/or total chlorine to assure the destruction of biological contaminants. It is also used just before distribution to assure enough disinfection residual remains throughout the distribution system to suppress the subsequent growth of bacterial and other biologicals.
Summary
Sodium hypochlorite fluid systems present unique challenges that can be overcome by using the proper thermoplastic material and following some simple installation practices. Preferred thermoplastic materials include PVC, CPVC, PVDF and PTFE with FKM elastomers for seals. For proper installation, remember to keep tanks and pumps out of the direct sunlight, use insulation where appropriate, and provide venting paths for outgassed vapors to escape the system.
David Guardia is the Technical Services Manager at Ryan Herco Flow Solutions. For more information, contact Ryan Herco Flow Solutions, 3010 North San Fernando Boulevard, Burbank, CA 91504 USA, phone (800) 848-1141, fax (818) 973-2670, www.rhfs.com